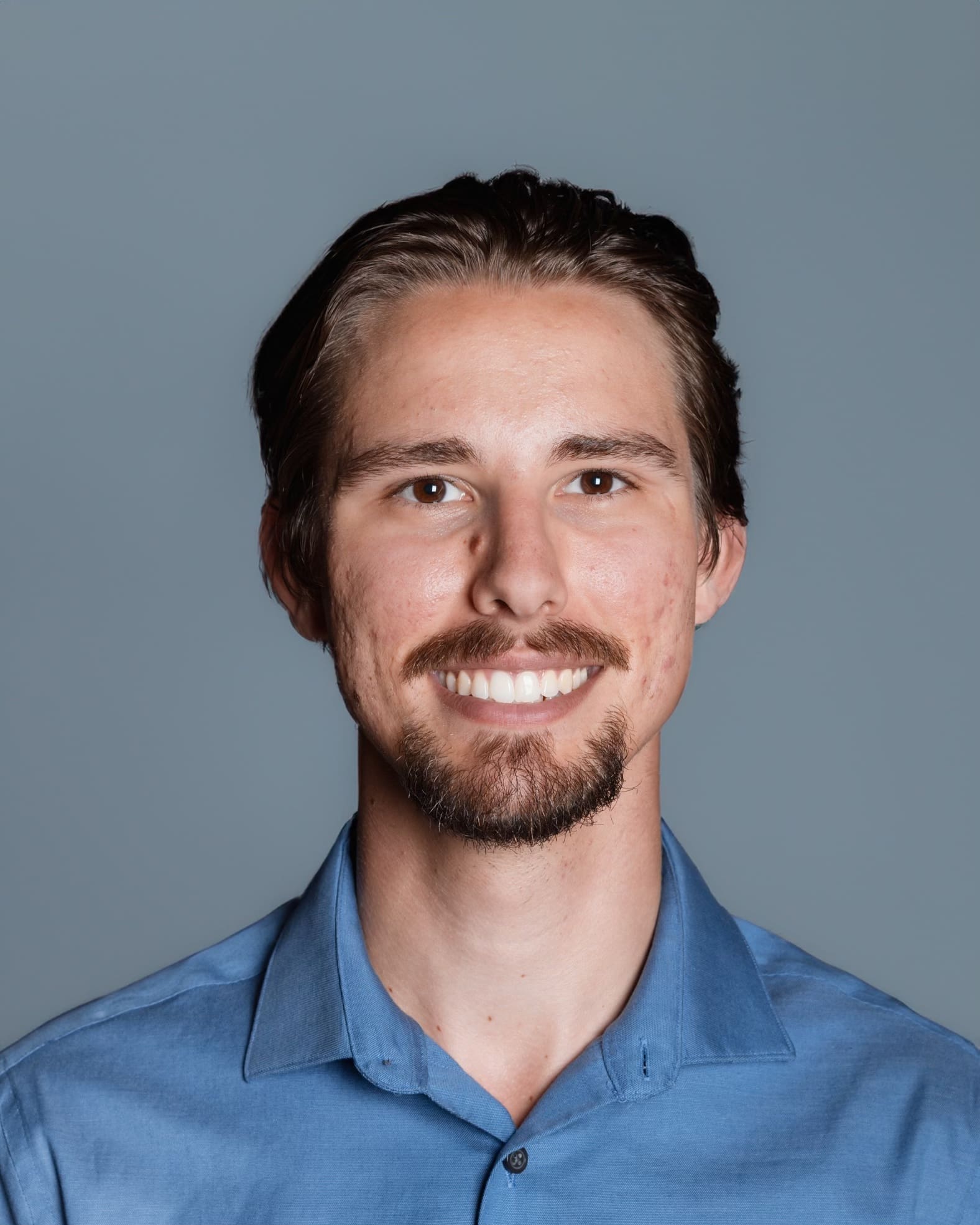
Benjamin Bazzle
- Owner & Founder
- Structural Welder
- Weld Test Supervisor
- Welding Instructor
I started my welding journey in 2017 when I attended a welding program for two years. In February 2019, I joined a local shipyard as a Structural Welder, where my job was to create and repair large metal structures, often for marine equipment. In 2021, I was promoted to Welding Instructor, where I taught:
- Flux Core Arc Welding (FCAW): A method that uses a wire-fed electrode to join metal, often used in heavy-duty applications due to its strength and efficiency. It includes options like high-strength flux core for demanding structural work and stainless steel 309 flux core for joining dissimilar metals.
- Gas Metal Arc Welding (GMAW) and Gas Metal Arc Welding Pulse (GMAW-P) on Aluminum: Commonly known as MIG welding, this technique uses an electric arc and a wire-fed electrode to join aluminum, which requires precision due to aluminum’s unique properties.
- Shielded Metal Arc Welding (SMAW): This welding method uses a flux-coated consumable electrode to create an electric arc that melts the electrode and base metal, fusing them together. Suitable for various metals, including stainless steel, the flux forms a protective slag to shield the weld. It’s ideal for structural work, repairs, and heavy-duty applications.
- Gas Tungsten Arc Welding (GTAW): This precise welding process uses a non-consumable tungsten electrode to create an arc, melting the base metal and filler material if added. Shielding gas, often argon, protects the weld from contamination. It’s ideal for thin metals, including stainless steel, aluminum, and copper-nickel, delivering clean, high-quality results.
- Air Carbon Arc Gouging (CAC-A): This process uses a carbon electrode to generate an electric arc that melts metal, which is then blown away by a high-velocity air stream. It’s commonly used for cutting, gouging, or removing welds, offering precision and efficiency in preparing or repairing metal surfaces in various applications.
- Oxyfuel Cutting: This cutting method uses a flame produced by burning a fuel gas with oxygen to heat the metal to its ignition point. Once the metal is heated, a stream of pure oxygen is directed onto the area, rapidly oxidizing and removing the metal, allowing for efficient and precise cuts on thick materials.
Also in 2021, I was promoted to Weld Test Supervisor. In this role, I oversaw all welding tests, ensuring that welders met industry standards and codes. Stringent testing requirements, including bend tests, macro-etch, Charpy V-notch, x-rays, penetrating dye, magnetic particle inspection, and ultrasounds, were used to detect imperfections inside the welds that might not be visible on the surface. Another aspect of my role was to write welding procedures according to company needs.
Outside the shipyard, I have a strong passion for custom metalwork. I’ve designed and built custom parts for motorcycles and worked on car and truck frames. Additionally, I have repaired marine equipment, including boat cranes and other essential machinery at a marina, combining both functional repairs and custom fabrications.
With my years of experience in structural welding, testing, and instruction, I am committed to ensuring high-quality work in both the industrial and custom metalwork fields, while also helping others develop the skills they need to succeed in the welding profession.